SOCIB glider engineers attended a course to manage “SeaGlider1K” refurbishment
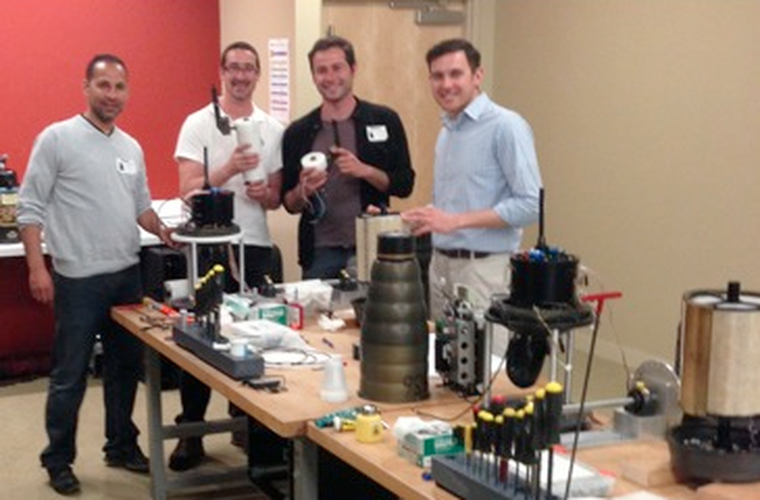
SOCIB's engineers, Simó Cusí and Marc Torner, have attended a training course at iRobot headquarters (Bedford, Massachusetts, USA) to obtain the official certification to refurbish “SeaGlider1K” gliders, celebrated from April 30th to May 2nd, 2013. Simó and Marc shared the class with two glider technicians from the French glider division of CNRS, the DT-INSU.
After this training course, SOCIB's technical glider staff is now capable of performing basic maintenance and refurbishment of its two units of SeaGlider1K gliders. Contrarily to the method followed with the Slocum model, the SeaGlider1K is by default returned to factory when maintenance is required, since the policy of the manufacturer, the iRobot Corporation®, does not allow users to disassemble the pressure resistant hull.
The three training sessions included the following tasks: (1) overview of the course, (2) review of the main assemblies of the SeaGlider1K, (3) full disassembly (see Figure 2) with battery and CTD sensor removal, (4) complete re-assembly, (5) mechanical and software checkout and, finally, (6) a simulation of the compass calibration procedure. Security measures and safety precautions were introduced throughout all these stages.
SOCIB stands now as one of the few groups in the world with the capability of partially servicing iRobot®'s SeaGlider1K, which in fact, will result in shorter out-of-service periods and a reduction in maintenance costs.